Understanding the Mechanics of Advanced Planning and Scheduling Software (APS)
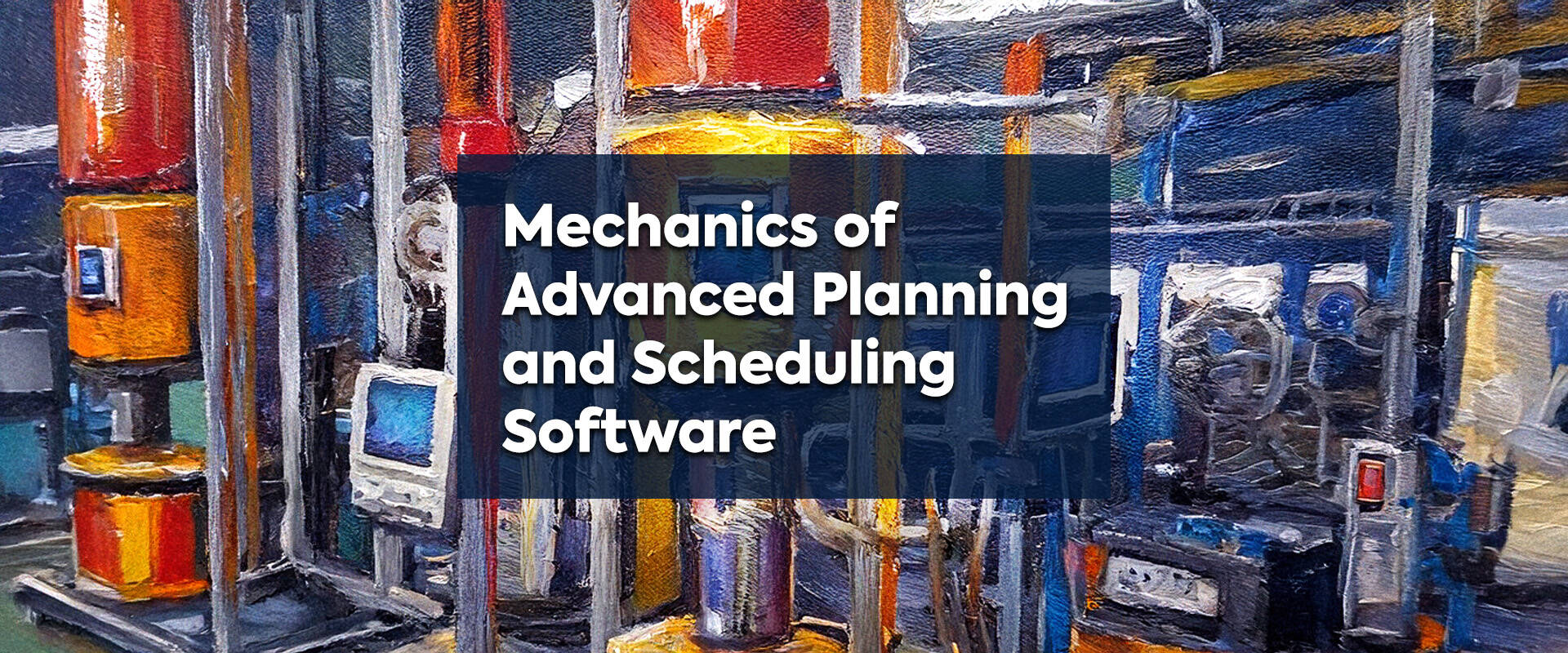
Introduction
Maintaining a competitive edge for manufacturing companies requires more than just skilled labor and the latest automated equipment. Strategic production planning is equally important, as it determines whether production can meet market demand as well as keep costs and delivery schedules in check.
Without a doubt, next-generation Advanced Planning and Scheduling (APS) software has become critical for businesses, helping manufacturers move beyond traditional methods to achieve streamlined, data-driven operations. By integrating information from multiple systems and applying highly developed algorithms, APS offers precise scheduling and real-time monitoring, setting a new standard for productivity and resilience in industries across the board.
How Does APS Software Work?
APS software operates using sophisticated algorithms and comprehensive data analysis to create and manage production schedules.
It follows a systematic approach that starts by gathering data from various manufacturing solutions, such as :
- Enterprise Resource Planning (ERP) systems
- Manufacturing Execution Systems (MES) platforms
- Floor-level operators
The APS software then utilizes its unique algorithms to analyze this data, revealing chances to optimize resource utilization while fulfilling customer orders.
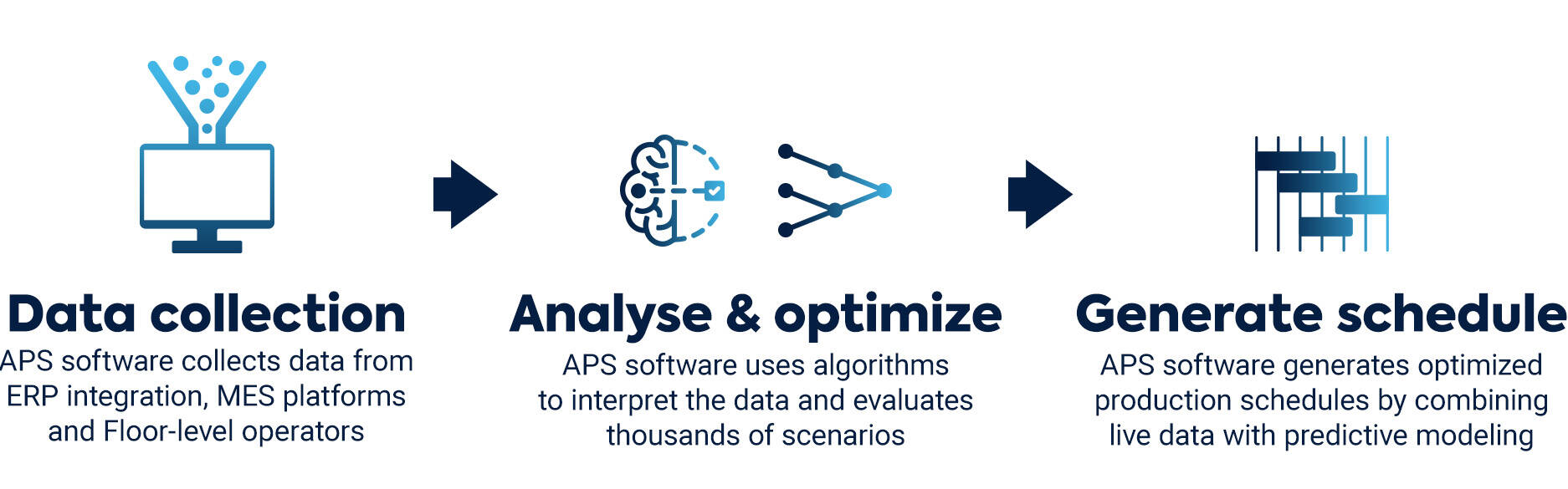
APS Data Collection
The first step in the APS process is data collection. APS software integrates information from multiple systems to provide users with a comprehensive view of their production processes.
- Through ERP integration, APS software gains access to real-time information on inventory levels, procurement schedules, and material availability. This data is indispensable so that workflows are aligned with available resources. For example, knowing the exact quantity of raw materials in stock allows APS to prevent delays caused by product shortages, keeping manufacturing timelines realistic and achievable.
- At the same time, MES platforms optimize throughput schedules and resource use. This data includes real-time production details (machine status, cycle times, production counts), work order information (status, start/end times, operational sequences), and resource availability (machine schedules, required maintenance, workforce availability).
- Floor-level operators also contribute relevant data, such as staffing, specific employee skills, and shift schedules. Machinery sensors generate operational metrics, including equipment reliability, maintenance flags, and downtime patterns. Quality data (inspection results, scrap rates, rework needs), stock levels (raw materials, work-in-progress, finished goods), and process parameters (machine settings, environmental conditions) are also gathered.
This broad spectrum of data forms the foundation for more agile production scheduling, making certain that no aspect of the production process is overlooked.
APS Analyses
Once the data is compiled, APS software uses algorithms to interpret it. These algorithms detect recurring production jams, operational inefficiencies, and underutilized resources.
APS software considers constraints such as equipment capacity and the resources required for production. By evaluating thousands of scenarios in a fraction of the time compared to traditional, often manual methods, APS identifies the most efficient course of action.
For example, contrary to spreadsheets, APS software might uncover that a particular machine consistently causes delays due to limitations during sales spikes. The software eliminates inefficiencies, improves output, and reduces costs by redistributing tasks to other machines or adjusting the production sequence. This level of analysis empowers manufacturers to make informed decisions quickly based on actionable insights.
APS Software and Schedule Optimization
The core function of APS software is to generate production schedules that align with business goals. These schedules are precision-built, taking into account variables such as deadlines, resource availability, and work orders. By combining live data with predictive modeling, APS creates schedules that maximize productivity and decrease waste.
Demand forecasting plays a critical role in this process. By analyzing historical trends and current market conditions, APS aligns production with anticipated needs.
For instance, if a seasonal surge in orders is expected, the APS software can adjust production volumes and allocate additional resources to keep up with sales.
Flexibility is another strength of APS scheduling. If unexpected disruptions occur, such as a machine breakdown or problems with vendors in the supply chain, the APS software can quickly adjust the production schedule, keeping everything on track.
Dynamic Capacity Planning with APS
Dynamic capacity planning is vital for optimizing production resources and meeting customer expectations. APS software equips manufacturers with tools to fine-tune their processes and enhance overall performance. By balancing project commitments across equipment and personnel, APS ensures resources are leveraged effectively, minimizing bottlenecks and maintaining smooth production flow.
Furthermore, APS software specializes in workforce planning by accurately predicting staffing needs and required skill sets for upcoming operations. This foresight helps manufacturers avoid setbacks like understaffing or overstaffing; as a result, teams are well-prepared to handle fluctuating workloads.
One compelling feature of APS software is its Available-to-Promise (ATP) capability, which empowers businesses to provide reliable delivery timelines. With precise scheduling and resource alignment, companies can boost customer confidence by consistently meeting commitments, fostering trust and long-term loyalty.
Real-time Production Monitoring with APS
During the execution phase, APS software continuously tracks the production schedules in real time. It tracks the progress of production activities, guaranteeing that everything is running according to plan.
For example, if a machine breaks down, the software can reschedule tasks to other available machines or adjust the production sequence to mitigate any idle time. The APS software can quickly revise the production plan to accommodate new orders at the last minute.
Conclusion
APS software transforms production management by integrating data, predictive analysis, and real-time oversight into one powerful system. By streamlining capacity planning, providing continuous monitoring, and facilitating agile responses, APS software empowers manufacturers to maintain business resilience in fast-paced industries, making it an indispensable tool for long-term profitability.
Wondering which APS platform is best suited for your company? Book a Syncrun APS software demo today to learn more about the value it can bring to the table.
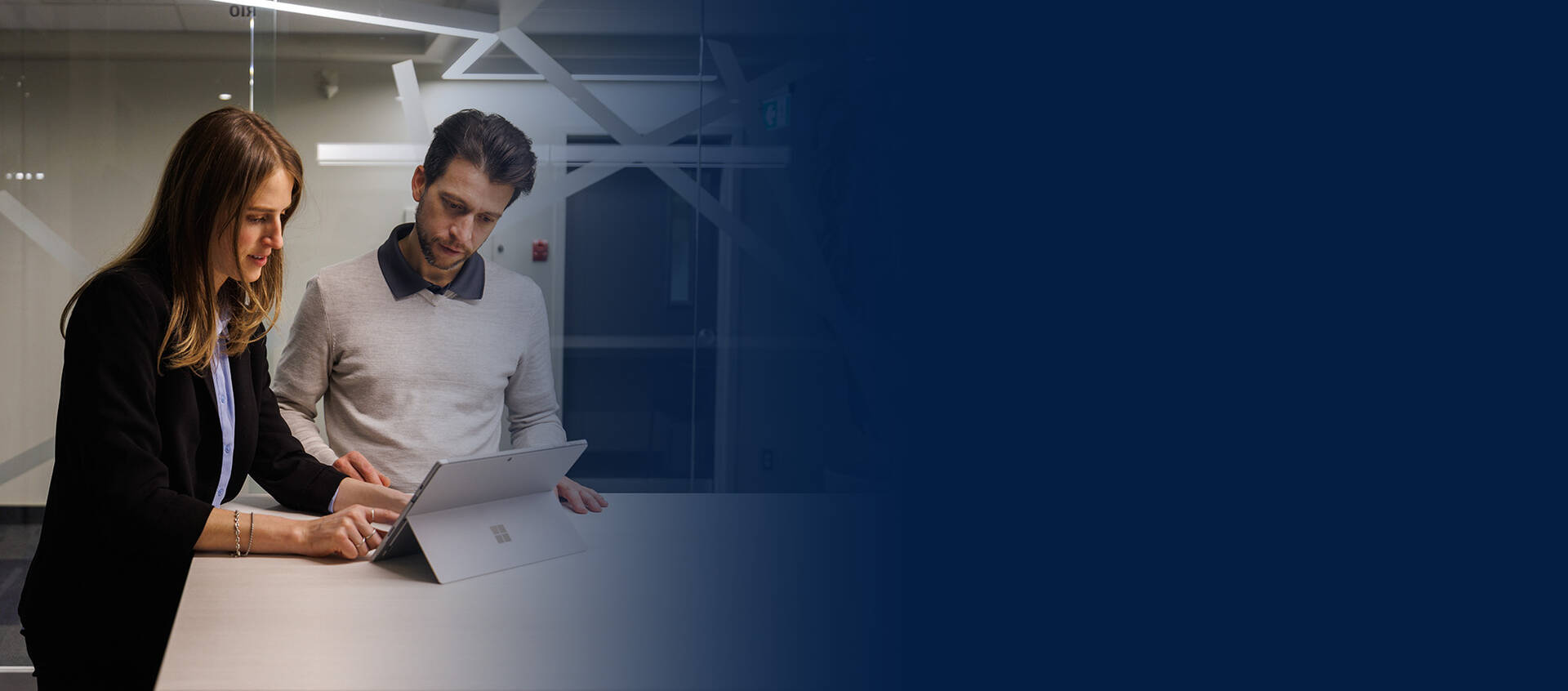
Join the Future of Manufacturing
Don’t get left behind in the rapidly evolving manufacturing industry 4.0. Partner with Premier Tech Digital and unlock the potential of Industry 4.0 with our solutions and expertise. Experience the future of manufacturing today!