The 4 core features of an Advanced Planning and Scheduling (APS) software
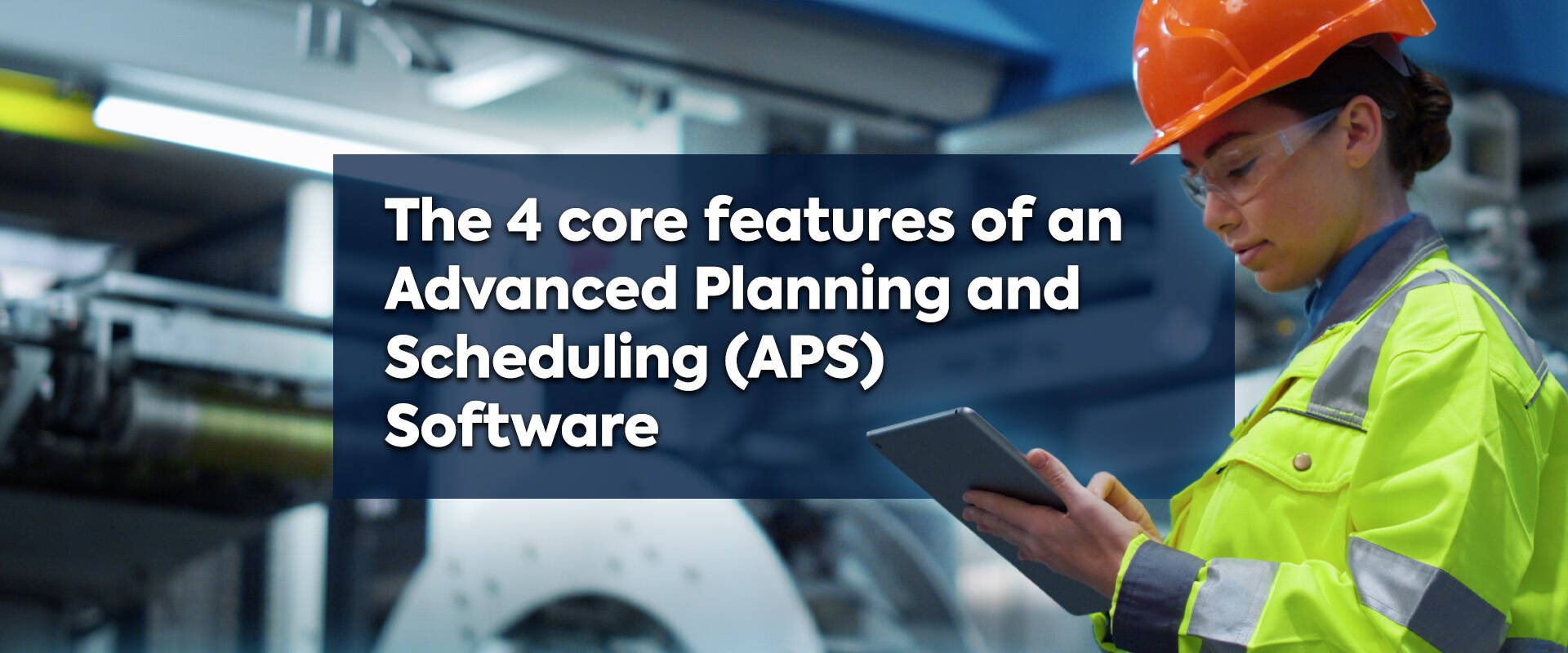
Introduction
Manufacturing today moves fast, and keeping up with customer demands means getting production planning just right. That’s where Advanced Planning and Scheduling (APS) software comes in—a powerful tool that’s changing the game for manufacturers and production planners.
APS software helps you make the most of your resources while navigating manufacturing constraints, making it easier to stay efficient and ahead of the curve. In this post, we’ll break down what makes APS software so impactful and how it can take your production planning and scheduling to the next level.
What Is APS Software?
Advanced Planning and Scheduling (APS) software is a powerful tool designed to help manufacturers and production planners streamline and optimize their production processes. By leveraging advanced algorithms and real-time data, APS software enables organizations to more accurately and efficiently schedule production timelines.
What sets APS apart is its ability to factor in a wide range of production challenges, such as labor availability, machine capacity, material supply, and delivery deadlines, making optimal use of available resources. This results in improved productivity, reduced downtimes, and better alignment with both organizational goals and customer expectations.
Whether it’s managing complex manufacturing workflows or adapting to unexpected changes in order inflow, APS software provides companies with the flexibility and control they need to stay competitive in their respective markets. More than simple planning, APS platforms give users the insights they need to make smarter decisions that drive bottom-line results.
Advanced Planning and Scheduling Software Key Features
APS software solutions offer an impressive array of features designed to tackle contemporary manufacturing issues, including resource bottlenecks, sales forecasting, supply chain disruptions, and the need for real-time operational adjustments to stave off costs.
But which features make the biggest impact? Let’s take a closer look at the key capabilities that set APS software apart and how they drive better production outcomes.
Operation Scheduling and Optimization
APS software relies on powerful multi-parameter engines to optimize how resources are used. It seamlessly coordinates raw material supplies, staff availability, skill sets, and subcontracting activities to keep production running without a hitch. By aligning every part of the process, an APS solution boosts productivity, reduces waste, and cuts costs.
What truly sets APS apart is its ability to adapt to change on the fly. Whether it’s unexpected equipment breakdowns, late shipments of raw materials, or last-minute customer order changes, APS can adjust production schedules almost instantly. This agility minimizes idle periods, maintains consistent output, and allows production teams to fulfill orders on time.
Another key strength of APS software is its proactive approach to managing deliveries. It simplifies tracking rush orders, giving users the means to visualize complex workflows and identify potential supply chain snags that may cause delays. By resolving these issues before they escalate, companies can consistently meet deadlines, respect service line agreements, improve customer satisfaction, and build a more reliable production process.
Capacity Planning
Efficient capacity planning is the backbone of manufacturing. Without it, companies risk overproducing low-priority items, missing out on high-margin opportunities, and incurring unnecessary expenses from rushed production, ultimately eroding profitability.
Take balancing workloads, for instance. APS software helps manufacturers distribute tasks evenly across resources—whether it’s machines on the production floor or specialized workers. Imagine a factory producing custom furniture: One week, an influx of large table orders might overload a specific assembly line while leaving other resources sparsely used. APS can substantially mitigate these types of manufacturing situations.
Workforce planning is another area where APS shines. Say a company needs to ramp up production for the holiday season. With APS, it’s easy to predict exactly how many team members will be needed and whether specific skills, like CNC machining or quality control expertise, are lacking. This means businesses can bring in temporary workers, schedule training, or better organize work rosters ahead of time, avoiding last-minute panic or costly overtime.
APS software also transforms how companies handle delivery commitments. For example, if a customer places an order for a large batch of products, some platforms provide an Available-to-Promise (ATP) feature that calculates an accurate delivery date by analyzing current inventory, production capacity, and upcoming orders. For example, a manufacturer of electric bicycles can confidently tell a distributor when its order will arrive—even during peak periods. This builds trust and ensures customers know exactly what to expect.
Real-time Monitoring
Monitoring and adjusting production plans is about staying on track—and the foundation of continuous improvement and effective operations management. APS generates comprehensive, real-time analytics into every aspect of the production process. With live data at their fingertips, managers can oversee progress against manufacturing key performance indicators (KPIs), spot inefficiencies, and intervene more quickly.
A case in point: APS software sheds light on potential delays caused by machine stoppages, material shortages, or personnel needs. By pinpointing these issues early, managers can proactively resolve roadblocks before they occur.
Managers can also assess cycle times, throughput, and equipment utilization rates for long-term strategic planning. If a particular shift consistently falls short of production targets, APS data can reveal whether the problem lies in human resources requirements, equipment performance, or workflow design. Therefore, decisions are based on cold, hard facts, not guesswork.
Simulation and Scenario Analyses
APS software gives businesses the tools to test different scenarios by creating a digital replica of their production processes. Whether it’s accounting for labor capacity, equipment maintenance calendars, or adapting to variable sales volume, these simulations help businesses explore the potential outcomes when making manufacturing changes. APS software provides a detailed comparison of these scenarios against existing plans. This data-driven tactic allows businesses to identify strategies that balance performance and cost-effectiveness while minimizing risks.
Consider a company that might accept a new production schedule that reduces lead times while rejecting a change that increases setup complexity. With this level of control, businesses can make informed, strategic decisions that improve operations without compromising other priorities.
Conclusion
Advanced Planning and Scheduling (APS) software is transforming the way manufacturers and production planners manage operations.
APS software redefines what’s possible in manufacturing. By implementing the right platform, a manufacturing business can increase both supply chain resilience and production control so that they can be more agile and adaptable in highly volatile industries.
Wondering which APS platform is best suited for your company? Book a Syncrun APS software demo today to learn more about the value it can bring to the table.
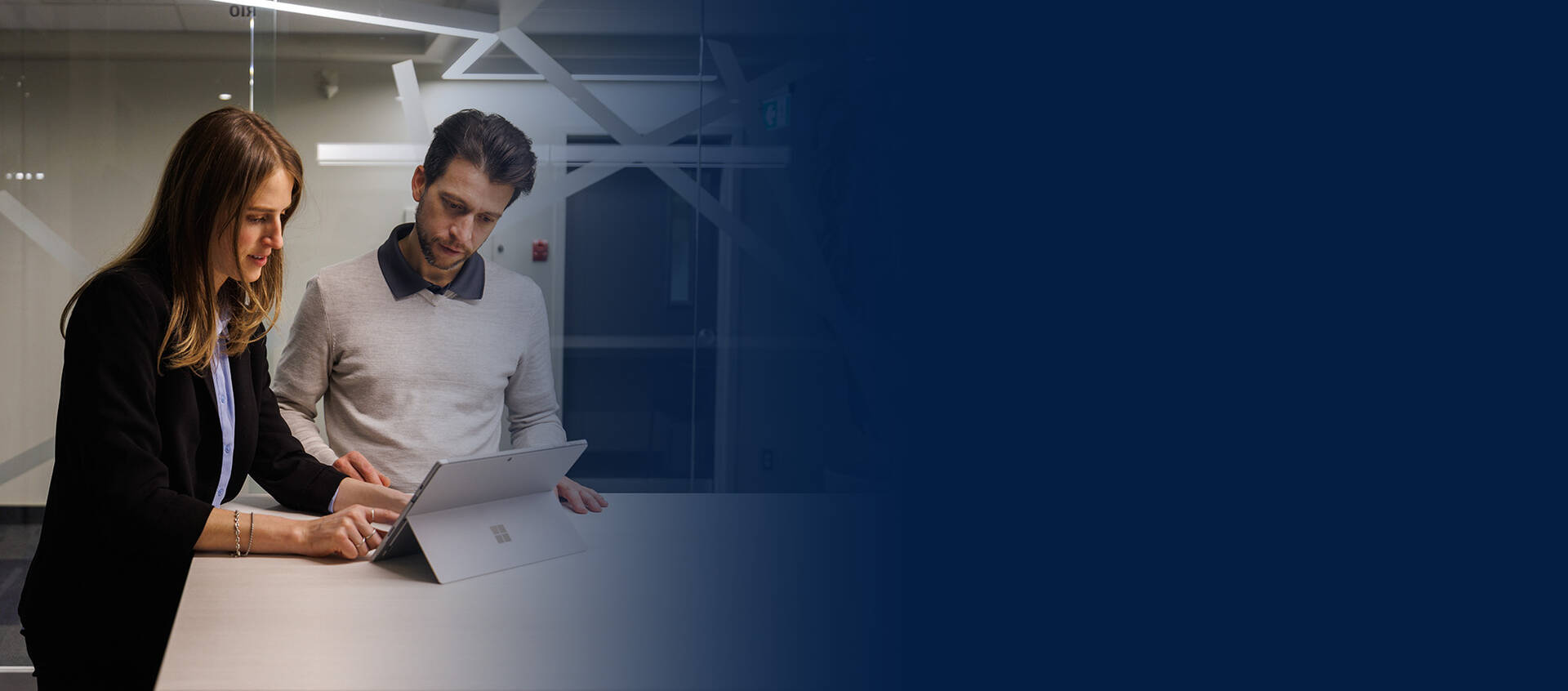
Join the Future of Manufacturing
Don’t get left behind in the rapidly evolving manufacturing industry 4.0. Partner with Premier Tech Digital and unlock the potential of Industry 4.0 with our solutions and expertise. Experience the future of manufacturing today!