CEVA Animal Health: Streamlining Production with an Enhanced Connectivity

CEVA Animal Health is a global leader in the animal pharmaceutical industry, with operations spanning across 42 countries and employing over 3,500 professionals. As part of its commitment to digital transformation, CEVA embarked on an ambitious project to streamline its production processes and improve quality control at its plant in Laval, France. The key objective was to digitalize the production lines and implement an effective in-process control (IPC) system. By leveraging Ignition software, CEVA aimed to enhance connectivity, automate data collection, and eliminate manual processes.
Challenges:
Prior to the implementation of Ignition software, CEVA faced several challenges in its production processes. CEVA sought out a digital solution to both centralize and systematize data capture, storage, and analysis.

Lack of reliable in-process control measurements:
One of the main concerns was that their production relied on manual in-process control (IPC) measurements. Therefore, a solution needed to include a reliable way to systematize and record IPCs that would replace the paper-reliant approach.
Time consuming analysis:
IPCs resulted in a significant volume of tickets and the long-term documentation and archiving of tickets quickly became problematic. To address these issues, the solution needed to provide a reliable infrastructure to record information, but also provide a means to save it for future reference.
Lack of a centralized overview:
Due to the nature of their strategy, CEVA lacked a centralized system and overview to manage sampling and in-process data. As such, they needed to equip their technicians with a solution that would enable them to have all their information in one place.
Lack of real-time correlation:
Finally, CEVA’s operation lacked a reliable way to proactively adjust for manufacturing constraints. Relying on paper-intensive batch reporting added to the challenges, where tickets were addressed 1-by-1 during, and after processing. This meant that faulty products could only be reliably detected after assessment, resulting in added backtracking and losses.
Finding a solution:
After a series of in-depth technical discussions with Premier Tech Digital to evaluate their requirements and objectives, CEVA opted for Ignition. Equipped with a hybrid solution and custom modules enabled them to have a secure store and backup of data. This configuration enabled them to reap many-a-reward, notably:
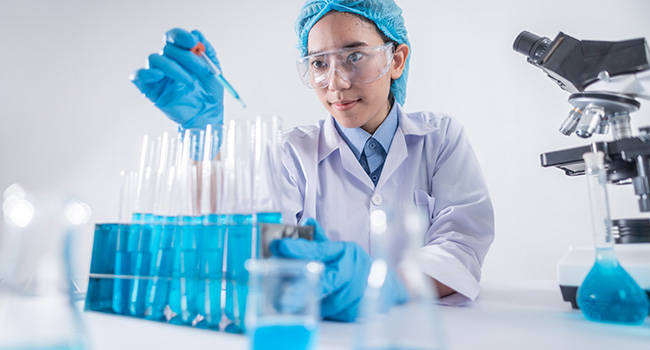
Enhanced Connectivity & Security:
The edge-PC served as a critical component in interconnecting the ecosystem's cloud, allowing for a real-time communication and save of data throughout their operation. The configuration, which favoured cybersecurity and data efficiency, enabled CEVA to master their data in a safe and reliable way.
Master Data Management:
A module was created within Ignition to combine recipes into an IPC-application. Without altering the in-process production, it ensured the accuracy of measures, as well as providing the right infrastructure for setting up a comprehensive archiving system.
Production Management:
Ignition’s batch control module allowed CEVA to organize production by batch number, product code, and version, providing a clear overview of the production status. This facilitated calibration, automated sampling, and real-time monitoring of production lines, ensuring reliable and efficient production processes.
Audit Trail and Compliance:
With comprehensive user-logging capabilities, the system organized data for future access, where production can be reviewed by filtering for a period, person, or workshop.
Results and Benefits:
By leveraging the power of connectivity, CEVA has revolutionized its production processes, enhancing efficiency, data integrity, and overall quality control. The integration of Ignition software has not only eliminated manual and time-consuming tasks but has also provided a robust platform for real-time monitoring, streamlined reporting, and comprehensive data analysis. As a result, CEVA has witnessed a significant boost in operational performance, cost savings, and compliance with regulatory standards.
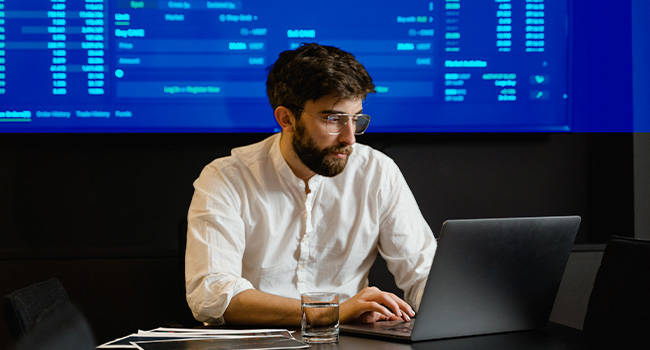
Data Integrity and Archiving:
Ignition's centralized system ensured data integrity, enabled CEVA to eliminate paper-based oversight, and provided a secure database for easy access to historical records
Improved Quality Control:
The real-time monitoring and alerts enabled prompt action to address deviations efficiently and ensures adherence to predefined parameters.
Increased Efficiency:
The digitalization of production processes and automated data collection reduced the risk of deviation and improved overall efficiency.
Enhanced Connectivity and Collaboration:
Ignition's web-based portal provided access to all employees, facilitating connectivity and collaboration across the organization.
Simplified Reporting:
The batch report generation module simplified the reporting process, reducing paper usage and saving time on documentation and archiving.
Conclusion:
Premier Tech Digital enabled CEVA to quickly integrate Ignition to their everyday operations and surmount their operational challenges. Utilizing a hybrid ecosystem, CEVA found itself empowered to manage and organize their data. Transparency helps address specific pain points within their production, like their heavy reliance on paper ticketing.
The digitization of IPCs and the standardization of digital reporting significantly improved sequencing, data integrity, and overall compliance. With an adaptable and scalable setup, CEVA achieved a more connected and digitally empowered manufacturing environment, setting up a foundation for their exciting next steps.
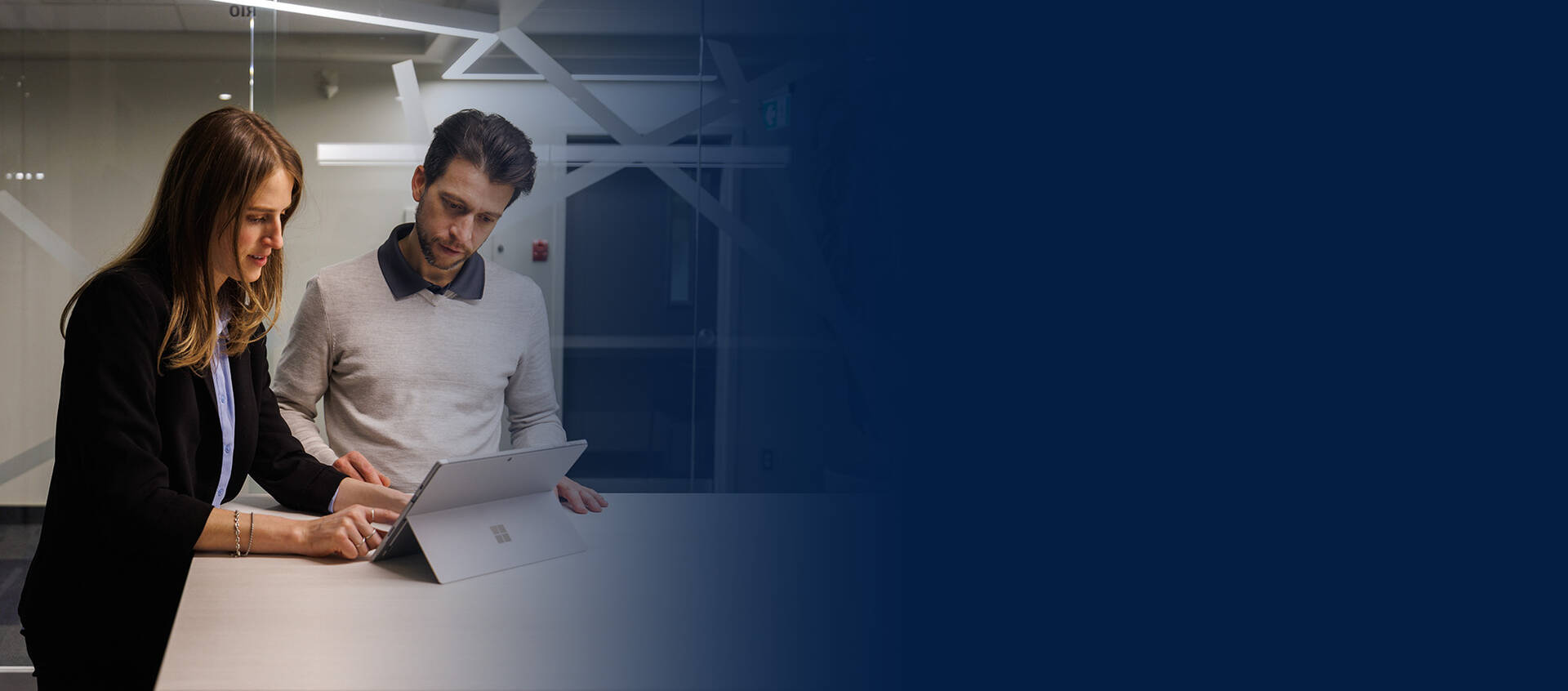
Join the Future of Manufacturing
Don’t get left behind in the rapidly evolving manufacturing industry 4.0. Partner with Premier Tech Digital and unlock the potential of Industry 4.0 with our solutions and expertise. Experience the future of manufacturing today!