Understanding Overall Equipment Effectiveness (OEE): A Comprehensive Guide
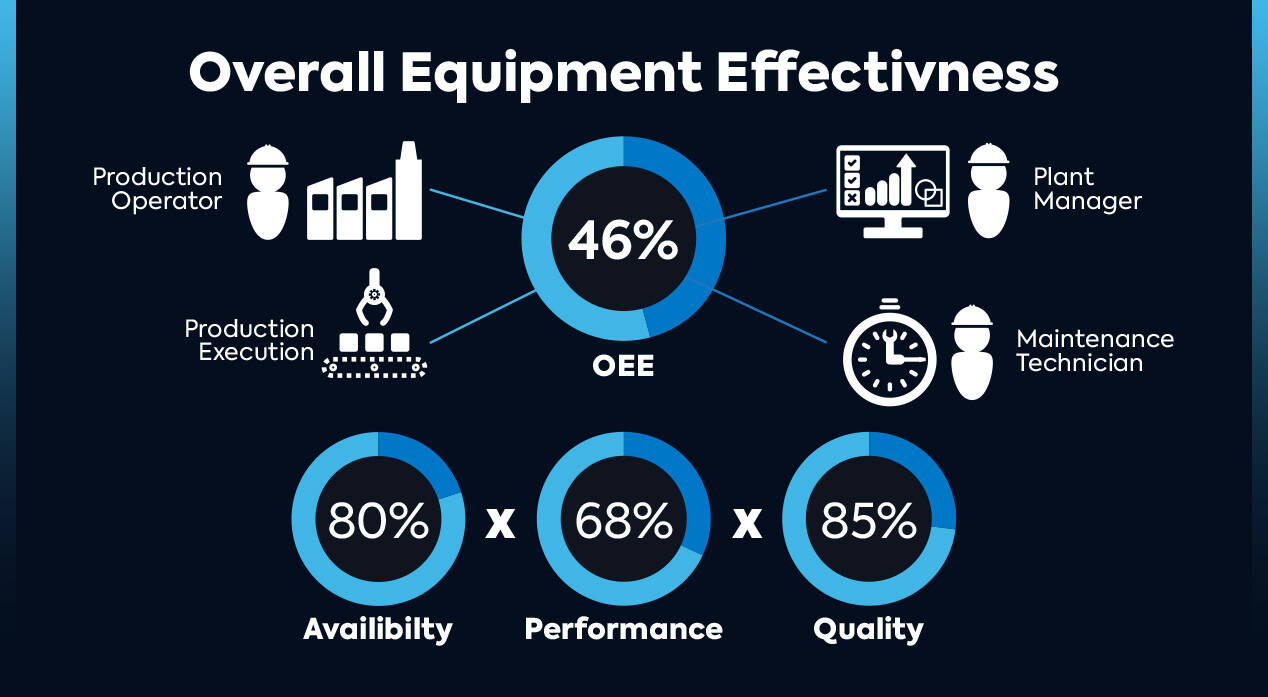
What is Overall Equipment Effectiveness (OEE)?
Overall Equipment Effectiveness (OEE) is a key performance metric used in manufacturing to evaluate how effectively equipment is utilized. It combines several aspects of production performance to provide a comprehensive view of equipment efficiency. This guide will explain what OEE is, how to calculate it, and best practices for improving it.
Defining OEE
Overall Equipment Effectiveness (OEE) is a metric that assesses the efficiency of manufacturing equipment. It measures how well equipment performs in terms of availability, speed, and quality. OEE provides insights into how effectively equipment is being used compared to its full potential.
Availability
Availability represents the proportion of scheduled time that the equipment is available to operate, as opposed to being down due to unplanned or planned stoppages. It is as simple as: if it was planned to run, did it actually run? It accounts for unplanned downtime such as machine breakdowns. High availability indicates that the equipment is operational and ready to produce for most of the planned time.
Performance
Performance is as simple as: when the equipment was actually running, was it producing at the rate it was supposed to or targeted to? It considers losses due to reduced speed, minor stoppages, or idling. If the equipment runs slower than its ideal cycle time, it negatively impacts the performance metric.
Quality
Quality measures the percentage of manufactured products that meet quality standards without requiring rework or being scrapped. A high-quality score means fewer defective units are produced, demonstrating consistent manufacturing accuracy and efficiency.
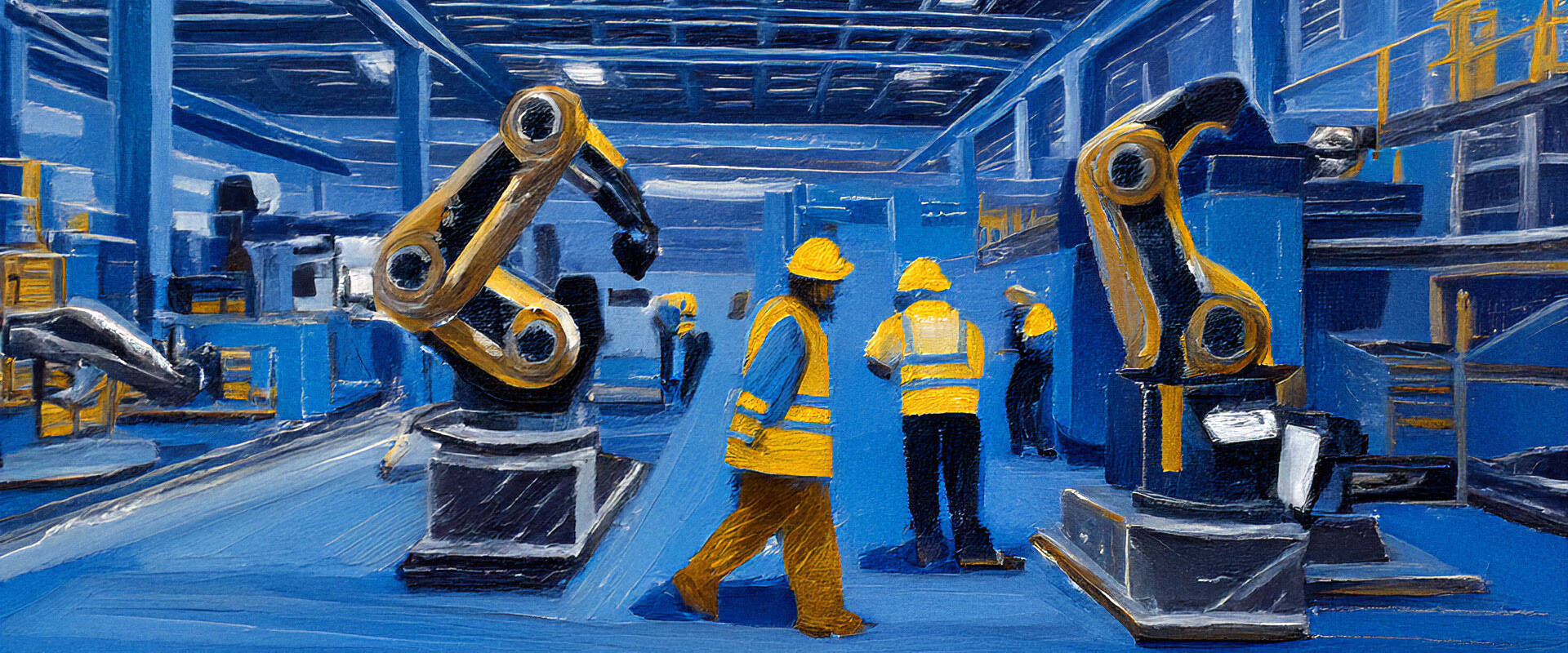
Who use OEE?
OEE is utilized by production managers, plant operators, and maintenance teams to monitor and improve production efficiency
Production Managers
Production managers are responsible for overseeing the entire production process and ensuring that performance goals are met. They utilize OEE (Overall Equipment Effectiveness) as a key performance indicator to identify areas for improvement and optimize production processes. By analyzing OEE data, production managers can make informed decisions to enhance efficiency, reduce downtime, and increase productivity.
-
Identifying Bottlenecks
If a production manager notices that a particular machine has consistently low availability, they can investigate the causes of downtime, such as frequent breakdowns or maintenance issues, and implement corrective actions to improve machine reliability.
-
Optimizing Production Schedules
By understanding the performance of each piece of equipment, production managers can optimize production schedules to ensure that high-performing machines are utilized effectively, and maintenance is scheduled during periods of low demand to minimize disruption.
-
Setting Performance Targets
Using OEE data, production managers can set realistic and achievable performance targets for the production team and track progress towards these goals.
Plant Operators
Plant operators are responsible for the day-to-day operation of machinery and equipment on the production floor. They use OEE to monitor daily equipment performance and ensure that machines are running at optimal capacity. By keeping a close eye on OEE metrics, plant operators can quickly identify and address issues that may affect production efficiency.
-
Monitoring Equipment Performance
Plant operators can use OEE dashboards to monitor real-time performance data, such as machine speed, cycle times, and downtime events. This allows them to take immediate action if they notice any deviations from the expected performance.
-
Reducing Minor Stoppages
If OEE data shows frequent minor stoppages, such as jams or adjustments, plant operators can investigate the root causes and implement solutions to reduce these interruptions and maintain steady production.
-
Ensuring Quality
By tracking the quality component of OEE, plant operators can identify trends in product defects or rework and take steps to improve quality control processes, ensuring that only high-quality products are produced.
Maintenance Teams
Maintenance teams play a crucial role in ensuring that equipment is well-maintained and operates efficiently. They leverage OEE to identify the most common or recurring downtimes that they can take action on. By analyzing OEE data, maintenance teams can prioritize maintenance activities, take corrective actions, and measure the impact of their interventions.
-
Prioritizing Maintenance Activities
By identifying equipment with low availability due to frequent breakdowns, maintenance teams can prioritize preventive maintenance tasks to address the most critical issues and prevent future downtime.
-
Measuring Impact of Actions
After performing maintenance activities, teams can use OEE data to measure the impact of their actions. For example, if a machine's availability improves after a specific maintenance task, it indicates a positive impact, which can be documented and repeated as necessary.
-
Continuous Improvement
Maintenance teams can use OEE data to feed the continuous improvement loop by regularly reviewing performance metrics, identifying areas for improvement, implementing corrective actions, and monitoring the results to ensure ongoing enhancements in equipment reliability and performance.
Importance of Calculating OEE
Maximizing Production Efficiency
By calculating Overall Equipment Effectiveness (OEE), companies can identify bottlenecks within their production processes, allowing them to take targeted actions to alleviate these constraints. This leads to a smoother workflow and higher production rates.
Additionally, OEE metrics help in reducing downtime by pinpointing the exact causes of equipment failures or inefficiencies. With this data, companies can implement proactive maintenance strategies and schedule maintenance activities during planned shutdowns, rather than experiencing unexpected breakdowns.
This proactive approach could extend the lifespan of the machinery but also ensures consistent production output and improves overall efficiency.
Identifying and Reducing Losses
Understanding OEE helps in identifying and reducing the six major losses in manufacturing: equipment failure, setup and adjustments, idling and minor stoppages, reduced speed, process defects, and reduced yield.
For example, if a company notices that the performance rate is consistently low, it can investigate further to find out if the issue is caused by suboptimal machine operation speeds or frequent minor stoppages.
Addressing these issues can lead to substantial improvements in throughput and overall productivity.
Enhancing Decision-Making
Moreover, OEE provides valuable data that enhances decision-making processes. With accurate OEE calculations, managers can prioritize investments in equipment upgrades, training programs, or process improvements.
For instance, if a specific production line consistently shows a low OEE, may justify the investment in new machinery or technology to solve bottle neck on the line.
Additionally, tracking OEE over time allows companies to measure the impact of implemented changes and continuously strive for operational excellence.
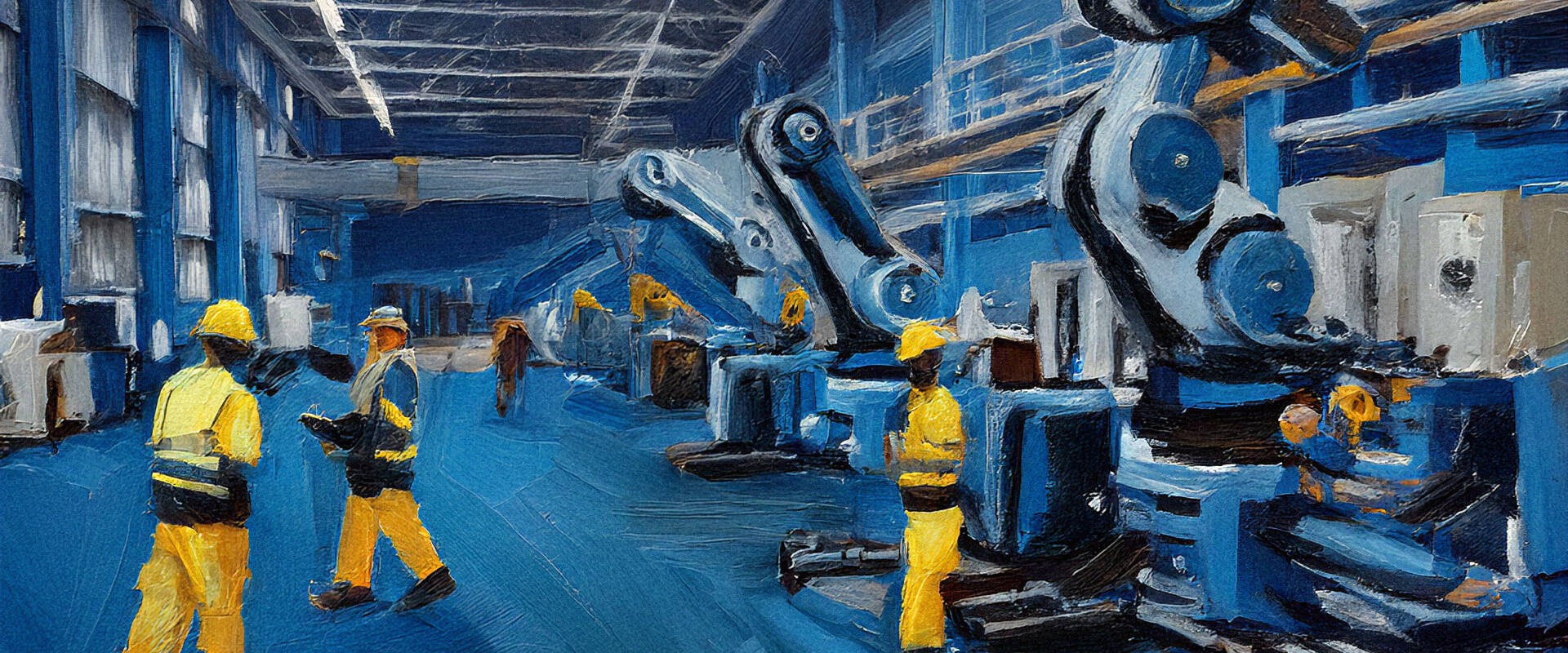
Calculating Availability
Operating Time: The time during which equipment is running.
Planned Production time: Total time the equipment is scheduled to operate.
Calculating Performance
Ideal Cycle Time: The fastest time to produce one unit.
Total Pieces produced: Number of units made during Actual Production Time.
Operating Time: The time during which equipment is running.
Calculating Quality
Good Units Produced: Units that meet quality criteria.
Total Units Produced: Total number of units manufactured.
Understanding OEE:
A Practical Example
Calculating Overall Equipment Effectiveness (OEE) is crucial for businesses aiming to maximize their production efficiency. We'll walk through a practical example of calculating OEE and discuss whether the resulting score is considered good, along with some tips on how to improve it.
Example:
Let's consider a manufacturing scenario with the following metrics:
- Availability: 80%
- Performance: 68%
- Quality: 85%
The formula for calculating OEE is:
Availability x Performance x Quality
Performing the calculation:
0.8 x 0.68 x 0.85
The result:
OEE = 46%
Is a 46% OEE Score Good?
To determine whether a 46% OEE score is good, we can refer to the following rules of thumb:
85% or higher
World-Class OEE
Indicates excellent performance across availability, performance, and quality.
60% to 84%
Good OEE
Shows that the production process is fairly effective but still has room for improvement.
40% to 59%
Average OEE
Suggests that there are significant areas for improvement in the production process.
Below 40%
Poor OEE
Indicates that there are major inefficiencies that need to be addressed urgently.
An OEE score of 46% falls into the "Average" category, suggesting that there is significant room for improvement across one or more of the three key factors: Availability, Performance, and Quality.
Improving Availability
Check for Downtime: Evaluate the reasons for equipment downtime. Are there frequent breakdowns, or is maintenance taking longer than expected?
Improve Scheduling: Ensure that maintenance activities are well-planned and that there is minimal disruption to production schedules.
Improving Performance
Analyze Speed Losses: Investigate why the equipment is not running at its maximum speed. Are there bottlenecks, or is there a need for operator training?
Optimize Processes: Look for inefficiencies in the production process that could be streamlined to improve overall speed.
Improving Quality
Reduce Defects: Examine the causes of defects in the produced items. Implement quality control measures to identify and fix issues early in the production process.
Enhance Training: Ensure operators are adequately trained to maintain high-quality standards and reduce errors.
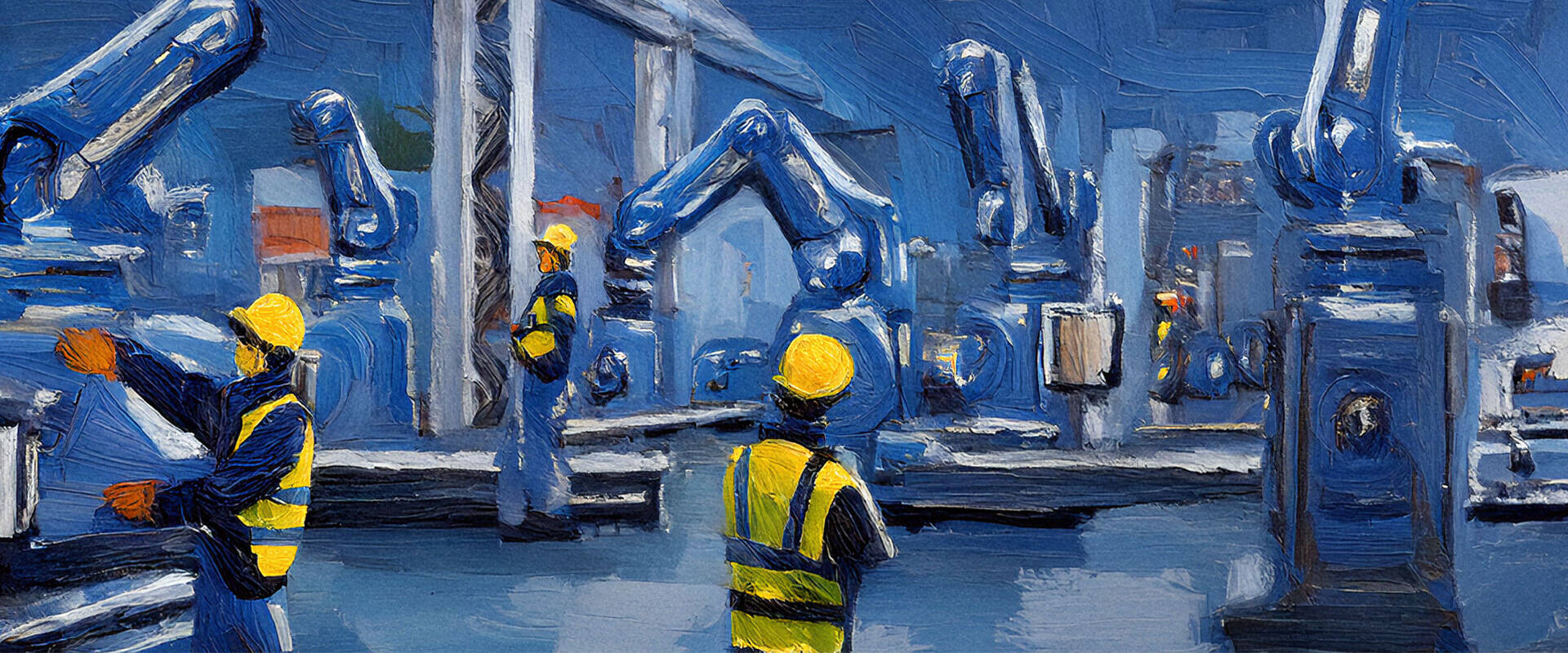
Is Increasing OEE Easy?
In theory, improving OEE might seem straightforward—just enhance availability, performance, and quality. However, in practice, it can be quite challenging due to several reasons:
-
Complexity of Operations
Manufacturing processes can be highly complex, involving numerous variables that interact in different ways. Identifying and addressing the root causes of inefficiencies requires a deep understanding of these processes.
-
Data Accuracy
Accurate and reliable data collection is crucial for measuring OEE and identifying areas for improvement. Inconsistent or inaccurate data can lead to misinformed decisions.
-
Resource Constraints
Implementing improvements often requires investment in new technologies, training, or process changes. Limited resources can be a significant barrier to making these investments.
-
Cultural Resistance
Changes in processes or practices may face resistance from employees who are accustomed to the existing way of doing things. Overcoming this resistance requires effective change management and communication.
-
Continuous Improvement
OEE improvement is not a one-time effort but a continuous process. Sustaining high OEE levels requires ongoing monitoring, analysis, and adjustments.
Conclusion
Overall Equipment Effectiveness (OEE) is a vital metric for assessing and improving manufacturing performance. By understanding how to calculate and interpret OEE, manufacturers can enhance equipment efficiency, reduce waste, and achieve better production outcomes.
With a Manufacturing Execution System (MES) like OpRize, these users can seamlessly track real-time data, optimize production processes, and ensure quality control throughout the entire manufacturing cycle.
Book a meeting here to learn more about OpRize, the MES powered by Premier Tech Digital | Smart Manufacturing, and discover how it can transform your production operations.
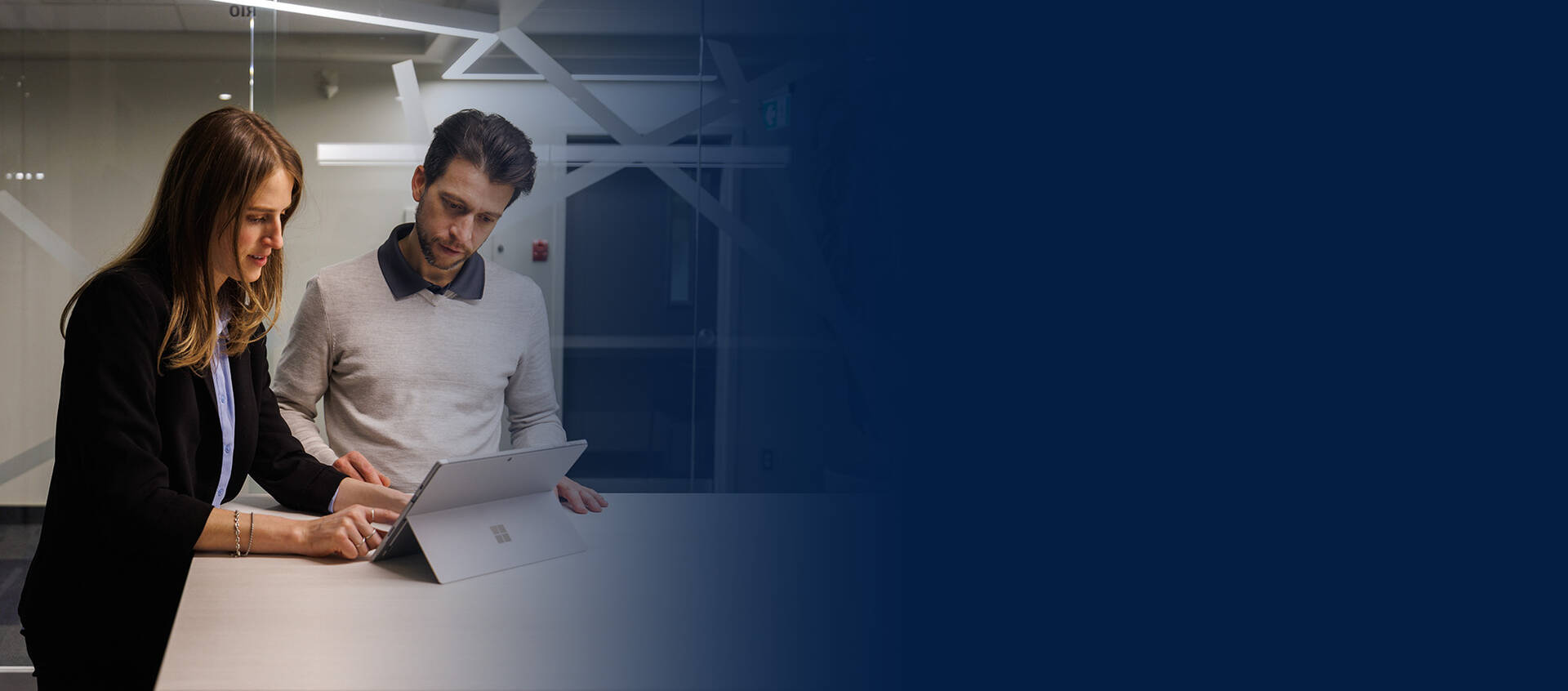
Join the Future of Manufacturing
Don’t get left behind in the rapidly evolving manufacturing industry 4.0. Partner with Premier Tech Digital and unlock the potential of Industry 4.0 with our solutions and expertise. Experience the future of manufacturing today!