MES vs ERP: How digital solutions work together

Nowadays, there exists a plethora of digital solutions to improve and optimize manufacturing operations. As any manufacturer can imagine, a greater need for production can result in complex problems forming quickly. To avert these possible complications, manufacturers have come to seek solutions that allow them to have a complete overview of the operation.
Two solutions typically distinguish themselves from the rest to grant a bird’s-eye view of the operation. These two are usually the Enterprise Resource Planning Software (ERP) and the Manufacturing Execution System (MES).
This is exactly what we attempt to clear up below.
While these two prominent solutions offer a range of functionalities, they are best used in conjunction. The complementary relationship between the data is what makes these tools so advantageous. At a glance, here are the main distinguishing factors of what each solution offers:
MES
- Production-level resource management and optimization (OEE)
- Label creation, tracking and genealogy records all of the steps within manufacturing
- Records and vulgarizes performance analytics, tracking downtime, KPIs, etc.
- Empowers quality assurance management
ERP
- Centralizes an executive understanding across the operation (BI, PLM, CRM)
- Improves financial planning and management (accounting, procurement, inventory, and orders)
- Synthesizes enterprise metrics for reporting and stakeholder presentations
- Grants an operational bird’s-eye view for production and resource management

Fundamentally, a MES works on a Manufacturing Process level. Its goal is to essentially maximize efficiency within the roles engineers and team members have on the actual factory floor – It empowers specialists to do what they do best.
With a MES, you can proactively adjust by keeping track of all the assets and variables within your operational digital ecosystem. From production management and workorder completion (from ERP connectivity), to full-depth quality tracking and genealogy, a MES grants you a comprehensive view of your operation.
Advantageously, it allows you to be proactive and preventive in adjusting for previously unforeseen complications in manufacturing processes. By compiling a constant stream of accurate production data and offering a simplified visual of all crucial tags, you can adjust procedures to maximize efficiency.
Essentially, an ERP works on the Enterprise Processes level. An ERP serves as a recording system of sorts, it will serve as an executive’s right hand for managing order fulfilment, finances, forecasting; basically, the bigger picture and desired outcome tracking. By integrating and automating business processes, you can eliminate redundancies and erroneous data that is typically due to lengthy manual entry.
There is also a great advantage to automating processes, whereby consolidating processes to a centralized system grants a substantial amount of time. This gain can be redirected to growth and sustaining strong partnerships by easily communicating the state of operations to intra-organizational parties and associates like stakeholders.
An ERP can grant a company a bird-eye view of their operation, and in turn allow it to operate more efficiently. It allows for an executive to explore the contributions of each functional subgroup and how they support the overall goal and vision.
The key differences are seen in how these two solutions offer complimentary points of view. In demystifying the limitations of these digital solutions, we can elucidate the relation straightforwardly: Where an ERP will often be the right arm of CEOs and other senior managers, whereas a MES will be utilized by operational engineers and plant managers.
This being said, both systems act in a symbiotic relationship. The ERP will manage the macro aspects of the operation and feed the MES information on workorders for example. On the other hand, the MES will manage micro aspects and forward information on stock versus production rates to the ERP.
Further, the MES will be the concretizing factor of the investment. From its gathered data, operations can be refined and adjusted to optimize production and maximize beneficial output. The MES is what ensures a return on investment. It is deemed the enabler as it leverages the 4.0 industry (IIOT) to automate, concretize and forward autmation control to the ERP.
In a nutshell, both systems act as one unit to overview, manage and proactively adjust a manufacturing plant operation.
Contact us and we can discover what solutions are right for you!
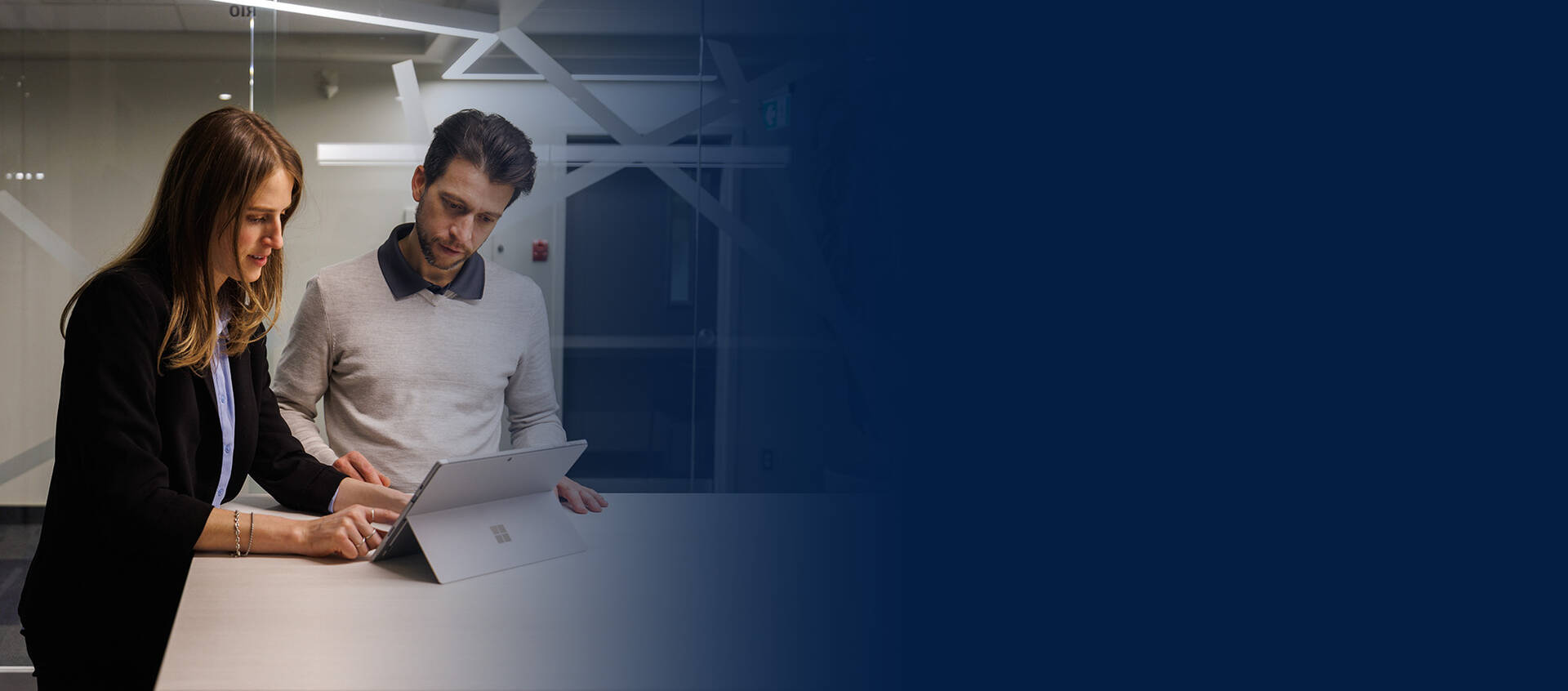
Join the Future of Manufacturing
Don’t get left behind in the rapidly evolving manufacturing industry 4.0. Partner with Premier Tech Digital and unlock the potential of Industry 4.0 with our solutions and expertise. Experience the future of manufacturing today!