Key KPIs to Track with a Manufacturing Execution System (MES)
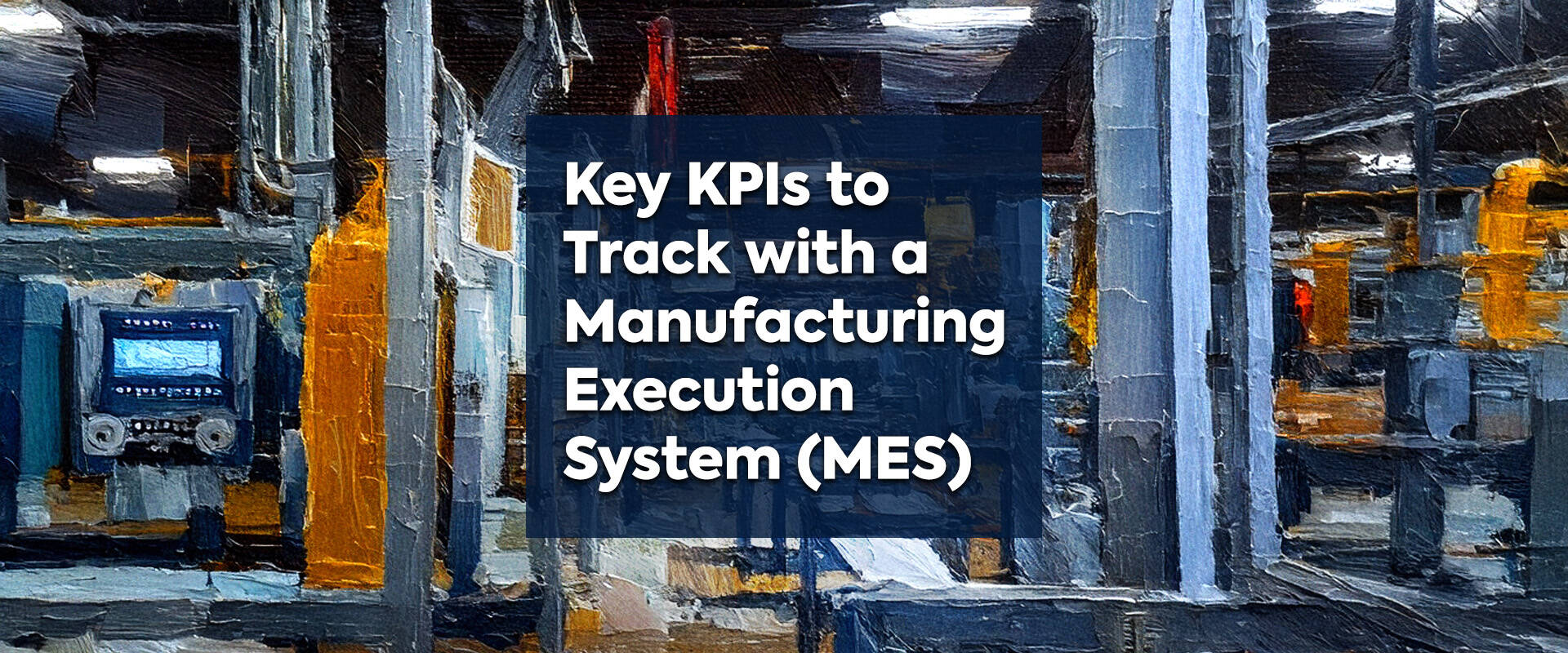
The Most Important KPIs to Track with a Manufacturing Execution System (MES)
Why Monitoring KPIs with an MES Matters
In modern manufacturing, real-time visibility is crucial for optimizing operations. A Manufacturing Execution System (MES) helps businesses collect and analyze critical data, enabling production managers, quality engineers, and plant directors to make informed decisions.
The real-time nature of an MES allows continuous improvement teams to immediately receive data to validate whether their process change had the positive impact they expected. By tracking key performance indicators (KPIs), manufacturers can improve efficiency, reduce waste, and ensure product quality.
Overall Equipment Effectiveness (OEE)
OEE is the gold standard for measuring manufacturing efficiency. It combines availability, performance, and quality into a single metric. Availability measures whether the equipment was actually running when it was supposed to be running, performance assesses production speed relative to the ideal cycle time and rates, and quality tracks the number of defect-free products. An MES provides real-time OEE monitoring, allowing operations managers to pinpoint inefficiencies and optimize production processes.
Downtime and Production Loss Analysis
Unplanned downtime can significantly impact production. An MES logs each downtime event, categorizes root causes, and helps maintenance teams implement preventive maintenance strategies to minimize disruptions. By analyzing trends in equipment failures and process bottlenecks, manufacturers can take proactive measures to prevent costly stoppages and maintain optimal workflow continuity.
Labor Productivity and Workforce Efficiency
An MES tracks operator performance, work center utilization, and resource efficiency. Plant managers use these insights to optimize workforce allocation and improve productivity. By analyzing real-time labor data, manufacturers can identify skill gaps, streamline work assignments, and ensure efficient labor distribution across shifts.
Production Throughput and Cycle Time
Throughput refers to the number of units produced per hour, while cycle time measures the time required to complete one unit. By tracking these KPIs, production supervisors can identify bottlenecks, streamline workflows, and enhance operational efficiency. A well-implemented MES enables real-time monitoring of these metrics, ensuring that production targets are consistently met while minimizing inefficiencies.
First Pass Yield (FPY) and Scrap Rate
FPY measures the percentage of defect-free products on the first attempt, while scrap rate calculates material waste during production. Quality managers rely on MES data to detect trends, reduce defects, and implement corrective actions. By closely monitoring these indicators, manufacturers can improve product consistency, lower production costs, and minimize rework.
Conclusion
The Manufacturing Execution System (MES), a powerful tool to optimize manufacturing production.
A Manufacturing Execution System (MES) is essential for tracking and optimizing key manufacturing KPIs. By leveraging real-time data, manufacturers can enhance efficiency, maintain high product quality, and drive continuous improvement across all departments.
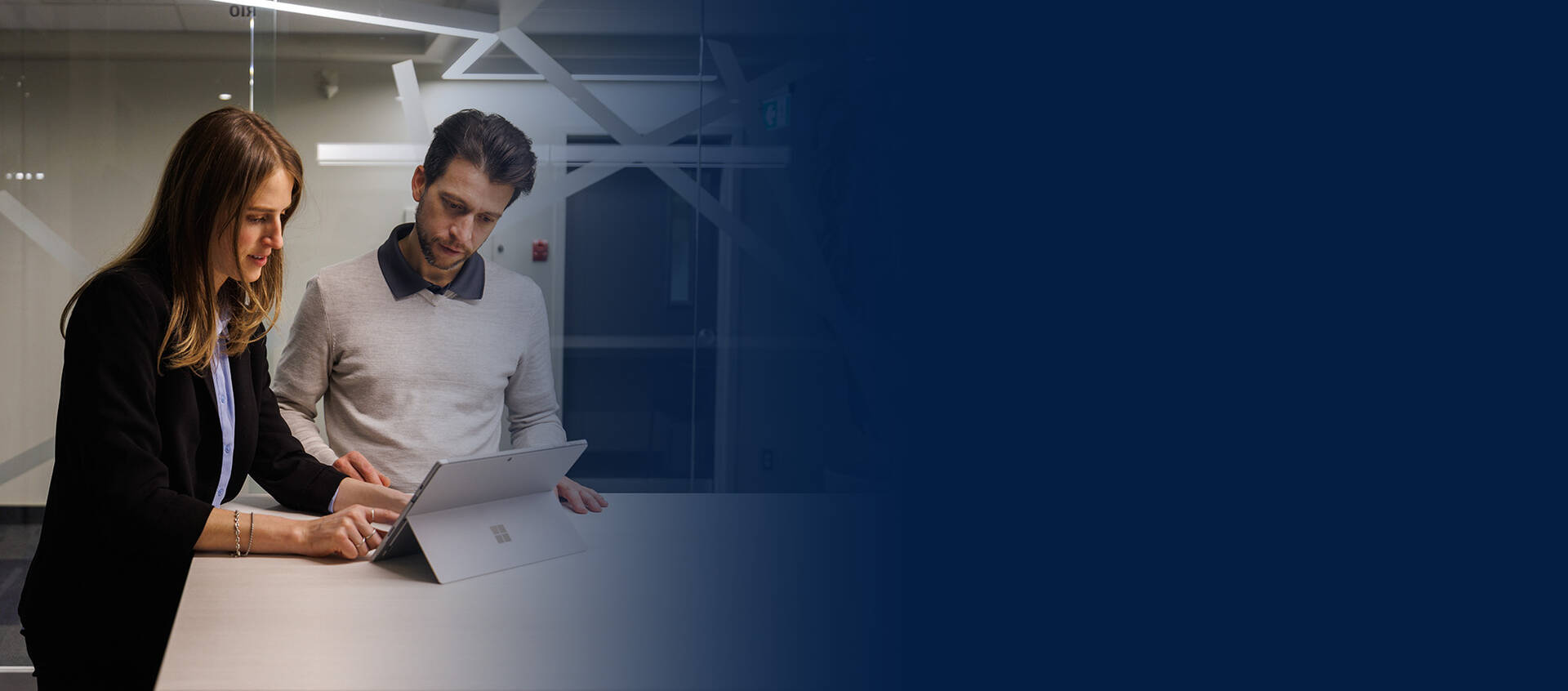
Join the Future of Manufacturing
Don’t get left behind in the rapidly evolving manufacturing industry 4.0. Partner with Premier Tech Digital and unlock the potential of Industry 4.0 with our solutions and expertise. Experience the future of manufacturing today!